Introduction of parallel twin screw extruder
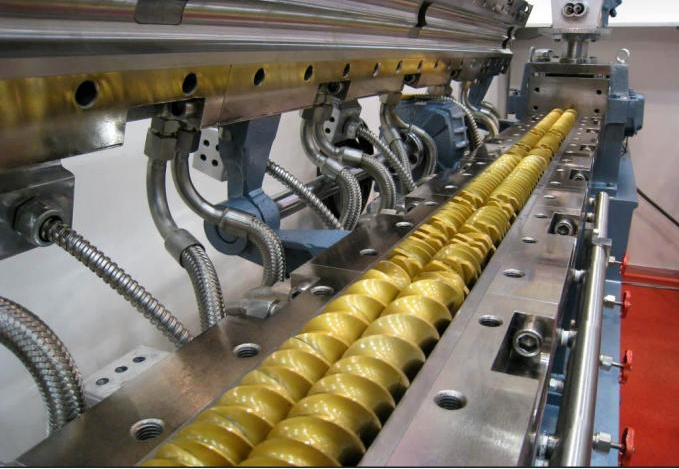
平双螺杆挤出机是在单螺杆挤出机基础上发展起来的,由于具有良好的加料性能、混炼塑化性能、排气性能、挤出稳定性等特点,目前已经广泛应用于挤出制品的成型加工。
Parallel twin-screw extruder is developed on the basis of single screw extruder. Due to its good feeding performance, mixing and plasticization performance, exhaust performance and extrusion stability, it has been widely used in the molding and processing of extruded products.
双螺杆挤出机的结构与类型:
Structure and type of twin screw extruder:
双螺杆挤出机由传动装置、加料装置、料筒和螺杆等几个部分组成,各部件的作用与单螺杆挤出机相似。与单螺杆挤出机的区别之处在于双螺杆挤出机中有两根平行的螺杆置于“∞” 形截面的机筒中。
用于型材挤出的双螺杆挤出机通常是紧密啮合且异向旋转的,虽然少数也有使用同向旋转式双螺杆挤出的,一般在比较低的螺杆速度下操作,约在10 r/min。高速啮合同向旋转式双螺杆出机,用于配混、排气或作为连续化学反应器,这类挤出机最大螺杆速度范围为300-600r/min。非啮合型挤出机用于混合、排气和化学反应,其输送机理与啮合型挤出机大不相同,比较接近于单螺杆挤出机的输送机理,二者有本质上的差别,从运动原理来看,双螺杆挤出机中同向啮合和异向啮合及非啮合型是不同的。
Twin screw extruder is composed of transmission device, feeding device, barrel and screw. The function of each component is similar to that of single screw extruder. The difference between twin-screw extruder and single screw extruder is that two parallel screws are placed in the barrel with "∞" section.
The twin-screw extruder used for profile extrusion is usually tightly meshed and rotating in different directions. Although a few also use co rotating twin-screw extrusion, it is generally operated at a relatively low screw speed, about 10 R / min. High speed intermeshing co rotating twin-screw extruder is used for mixing, exhaust or as a continuous chemical reactor. The maximum screw speed range of this kind of extruder is 300-600r / min. The non meshing extruder is used for mixing, exhaust and chemical reaction. Its conveying mechanism is very different from that of the meshing extruder, which is close to the conveying mechanism of the single screw extruder. They are essentially different. From the perspective of motion principle, the co meshing, non meshing and non meshing types in the twin screw extruder are different.
1、同向啮合型双螺杆挤出机:这类挤出机有低速和高速两种,前者主要用于型材挤出,而后者用于特种聚合物加工操作。(1)紧密啮合式挤出机。低速挤出机具有紧密啮合式螺杆几何形状,其中一根螺杆的螺棱外形与另一根螺杆的螺棱外形紧密配合,即共轭螺杆外形。
(2)自洁式挤出机。高速同向挤出机具有紧密匹配的螺棱外形。可将这种螺杆设计成具有相当小的螺杆间隙,使螺杆具有密闭式自洁作用,这种双螺杆挤出机称为紧密自洁同向旋转式双螺杆挤出机。
2、异向啮合型双螺杆挤出机:紧密啮合异向旋转式双螺杆挤出机的两螺杆螺槽之间的空隙很小(比同向啮合型双螺杆挤出机中的空隙小很多),因此可达到正向的输送特性。
3、非啮合型双螺杆挤出机:非啮合型双螺杆挤出机的两根螺杆之间的中心距大于两螺杆半径之和。
1. Co rotating meshing twin screw extruder: this kind of extruder has two types: low speed and high speed. The former is mainly used for profile extrusion, while the latter is used for special polymer processing operation.
(1) Tight meshing extruder. The low-speed extruder has a tight meshing screw geometry, in which the screw edge shape of one screw is closely matched with the screw edge shape of the other screw, that is, the conjugate screw shape.
(2) Self cleaning extruder. The high-speed co rotating extruder has a closely matched screw edge shape. This kind of screw can be designed with quite small screw clearance to make the screw have closed self-cleaning effect. This kind of twin-screw extruder is called close self-cleaning co rotating twin-screw extruder.
2. Counter meshing twin-screw extruder: the gap between the two screw grooves of the tightly meshing counter rotating twin-screw extruder is very small (much smaller than that in the co meshing twin-screw extruder), so it can achieve positive conveying characteristics.
3. Non meshing twin screw extruder: the center distance between the two screws of the non meshing twin screw extruder is greater than the sum of the radius of the two screws
双螺杆挤出机的优点:
Advantages of twin screw extruder:
磨损情况:由于打开方便,所以能随时发现螺纹元件、机筒内衬套的磨损程度,从而进行有效的维修或更换。不至于在挤出产品出现问题时才发现,造成不必要的浪费。
降低生产成本:制造母粒时,经常需要更换颜色,如果有必要更换产品,在数分钟时间内打开开启式的加工区域,另外还可通过观察整个螺杆上的熔体剖面来对混合过程进行分析。目前普通的双螺杆挤出机在更换颜色时,需要用大量的清机料进行清机,既费时、费电,又浪费原材料。而剖分式双螺杆挤出机则可解决这个问题,更换颜色时,只要几分钟时间就可快速打开机筒,进行人工清洗,这样就可不用或少用清洗料,节约了成本。
提高劳动效率:在设备维修时,普通的双螺杆挤出机经常要先把加热、冷却系统拆下,然后再整体抽出螺杆。而剖分式双螺杆则不用,只要松开几个螺栓,转动蜗轮箱手柄装置抬起上半部分机筒即可打开整个机筒,然后进行维修。这样既缩短了维修时间,也降低了劳动强度。
高扭矩、高转速:目前,世界上双螺杆挤出机的发展趋势是向高扭矩、高转速、低能耗方向发展,高转速带来的效果即是高生产率。剖分式双螺杆挤出机即属于这个范畴,它的转速可达600转/分钟。所以在加工高粘度、热敏性物料方面具有独特的优势。
应用范围广:应用范围广泛,可适用于多种物料的加工
高产量、 高质量:具有普通的双螺杆挤出机所具有的其它优点,可实现高产量、 高质量、高效率、低能耗。
Wear condition: due to the convenient opening, the wear degree of threaded elements and bushing in the barrel can be found at any time, so as to carry out effective maintenance or replacement. It will not be found when there are problems in the extruded products, resulting in unnecessary waste.
Reduce production cost: when manufacturing masterbatch, it is often necessary to change the color. If it is necessary to change the product, open the open processing area within a few minutes. In addition, the mixing process can be analyzed by observing the melt profile on the whole screw. At present, when changing the color of ordinary twin-screw extruder, a large number of cleaning materials need to be used for cleaning, which is not only time-consuming, power consuming, but also a waste of raw materials. The split twin-screw extruder can solve this problem. When changing the color, the barrel can be quickly opened for manual cleaning in a few minutes, so that the cleaning material can be used without or less, saving the cost.
Improve labor efficiency: during equipment maintenance, ordinary twin-screw extruder often needs to remove the heating and cooling system first, and then extract the screw as a whole. The split twin-screw is not needed. Just loosen a few bolts, rotate the handle device of the worm gear box, lift the upper half of the barrel, and then open the whole barrel for maintenance. This not only shortens the maintenance time, but also reduces the labor intensity.
High torque and high speed: at present, the development trend of twin-screw extruder in the world is to develop towards high torque, high speed and low energy consumption. The effect of high speed is high productivity. Split twin-screw extruder belongs to this category, and its speed can reach 600 rpm. Therefore, it has unique advantages in processing high viscosity and heat sensitive materials.
Wide range of application: it has a wide range of applications and can be applied to the processing of a variety of materials
High output and high quality: it has other advantages of ordinary twin-screw extruder, and can realize high output, high quality, high efficiency and low energy consumption.
双螺杆挤出机和单螺杆挤出机的区别:Difference between twin screw extruder and single screw extruder:
物料的传送方式:在单螺杆挤出机中,固体输送段中为摩擦拖拽,熔体输送段中为黏性拖拽。固体物料的摩擦性能和熔融物料的黏性决定了输送行为。如有些物料摩擦性能不良,如果不解决喂料问题,则较难将物料喂入单螺杆挤出机。而在双螺杆挤出机中,特别是啮合型双螺杆挤出机,物料的传送在某种程度上是正向位移传送,正向位移的程度取决于一根螺杆的螺棱与另一根螺杆的相对螺槽的接近程度。紧密啮合异向旋转挤出机的螺杆几何形状能得到高度的正向位移输送特性。
物料的流动速度场:目前对物料在单螺杆挤出机中的流动速度分布已描述得相当明确,而在双螺杆挤出机中物料的流动速度分布情况相当复杂且难以描述。许多研究人员只是不考虑啮合区的物料流动情况来分析物料的流动速度场,但这些分析结果与实际情况相差很大。因为双螺杆挤出机的混合特性和总体行为主要取决于发生在啮合区的漏流,然而啮合区中的流动情况相当复杂。双螺杆挤出机中物料的复杂流谱在宏观上表现出单螺杆挤出机无法媲美的优点,例如,混合充分,热传递良好,熔融能力大,排气能力强及对物料温度控制良好等。
Material conveying mode: in the single screw extruder, friction drag is used in the solid conveying section and viscous drag is used in the melt conveying section. The friction properties of solid materials and the viscosity of molten materials determine the conveying behavior. If some materials have poor friction performance, it is difficult to feed the materials into the single screw extruder if the feeding problem is not solved. In the twin-screw extruder, especially the meshing twin-screw extruder, the material transmission is positive displacement transmission to some extent. The degree of positive displacement depends on the proximity between the screw edge of one screw and the relative screw groove of the other screw. The screw geometry of close meshing counter rotating extruder can obtain high positive displacement conveying characteristics.
Flow velocity field of materials: at present, the flow velocity distribution of materials in single screw extruder has been described quite clearly, while the flow velocity distribution of materials in twin screw extruder is quite complex and difficult to describe. Many researchers only analyze the material flow velocity field without considering the material flow in the meshing area, but these analysis results are very different from the actual situation. Because the mixing characteristics and overall behavior of Twin-screw Extruder mainly depend on the leakage flow in the meshing area, but the flow in the meshing area is very complex. The complex flow spectrum of materials in twin-screw extruder shows the incomparable advantages of single screw extruder, such as full mixing, good heat transfer, large melting capacity, strong exhaust capacity and good control of material temperature.
金韦尔机械针对不同原料对螺纹组合模式进行了优化,独立开发了包括免结晶PET平双排气式挤出机、PVC平行双螺杆挤出机、XPS二氧化碳发泡平双挤出机等多种机型。详情请咨询销售工程师:18913797098Gwell machinery has optimized the thread combination mode for different raw materials and independently developed a variety of models, including crystallization free pet flat double exhaust extruder, PVC parallel twin screw extruder, XPS carbon dioxide foaming flat double extruder and so on. For details, please consult the sales engineer: 18913797098